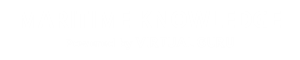
Marine Diesel Engine
1. MARINE ENGINE NOMENCLATURE & ENGINE RELATED TERMS
1. MAN B&W MARINE ENGINE NOMENCLATURE
Built-up by association of the German Engine builders MAN and their Danish Counterpart Burmeister & Wain between the period 1980 and 1982. MC engines were brought as a class of refined engines characterised by uniflow scavenging with hydraulic push rod operated exhaust valves on top of the cylinder. The engine types of MC programme are identified by the flowing letters and figures (marine engine nomenclature):
3. SOME COMMON TERMS
1. MARINE ENGINE CYCLES
These cycles use air as the working substance and the mass of air is assumed to remain constant. The theoretical cycles consider no induction or exhaust processes, only heat is added at one part of the cycle and rejected at another. No actual cycle operates that strictly follows the theoretical cycle.
2. OTTO CYCLE
.
4. DUAL COMBUSTION CYCLE
3. MARINE ENGINE STROKES
1. BASIC TERMS RELATED TO MARINE ENGINE STROKE
2. TIMING DIAGRAM
2.1. TWO STROKE ENGINES
2.2. FOUR STROKE ENGINES
3. TWO-STROKE VS. FOUR-STROKE ENGINES
3.1. DIFFERENCE BETWEEN 2-STROKE & 4-STROKE ENGINES
4. STROKE TO BORE RATION CLASSIFICATION
5. ADVANTAGES OF SUPER LONG STROKE
2 ) Design /sketches of main parts of diesel engine cylinder liner ,Piston oil cooled & water cooled ,Piston rod,Connecting Rod,Crosshead& bearing ,Bottom end bearing ,Connecting Rod bolts,Piston cooling arrangement.
A.MAIN ENGINE:
1 ) Construction of a 2 stroke Cross head type Diesel Engine.
1. Exhaust valve.
2. Fuel Injector.
3. Cylinder cover
4. Tie bolts/Tie rods
5. Crosshead
6. Connecting Rod
7. Liner
8. Piston
9. Piston Ring
10. Crankshaft
11. Camshaft
12. Frame box/A-Frame
13. Entablature/Cylinder Block
14. Bedplate
1. Exhaust Valve
Construction of Two-Stroke Marine Diesel engines has a single exhaust valve mounted in the centre of the cylinder head.
Exhaust valves open inwards into the cylinder so that the gas pressure in the cylinder will ensure positive closing and help dislodge any build-up of carbon on the valve seat.
The opening and closing of the valve is controlled by a cam mounted on the camshaft.
Modern two-stroke marine crosshead engines have a hydraulically operated air spring exhaust valve.
The cam operates a hydraulic pump, (instead of a push rod in older engines). Oil from the engine LO system displaced by the pump operates a piston in the exhaust valve which pushes the valve open.
Instead of mechanical spring the valve has an “air spring”.
Air at 7 bar is led via a non-return valve to the underside of the piston attached to the valve spindle. As the valve opens the air underneath the piston compresses.
When the hydraulic pressure relieves, the expansion of this compressed air assists in the closing of the valve.
Air is also led down the exhaust valve guide, this keeps the guide cool and prevents exhaust valve leaking up the guide.
The valve spindle equips with a winged valve rotator. The kinetic energy in the exhaust gas rotates the valve by a small amount as it passes. This keeps the valve at an even temperature and helps reduce the buildup of deposits.
The cage and the guide of the exhaust valve are of cast iron and arranged for water cooling. The housing is provided with a renewable seat made of hardened molybdenum steel.
The spindle or valve stem has made of heat resistant steel with stellite welded on to the seat.
In new designs, Nimonic (Nickel, Chromium, Cobalt) valves combined with proper seat cooling have yielded excellent service behaviour and long life.
List of components of the exhaust valve and their material (This question was asked to me in my interview)
2. Fuel Injector
The function of the fuel injection system in Two-Stroke Marine Diesel Engine Construction is to provide the right amount of fuel at the right moment and in a suitable condition for the combustion process.
The fuel injector is of 2 basic parts of the nozzle and nozzle holder or body.
The high-pressure fuel enters and travels down the passage in the body and then into the nozzle surrounding the needle valve. The needle valve is held closed on a seat by an intermediate spindle and a spring in the injector body.
The spring pressure and hence the opening pressure is set by compression nut which acts on the spring.
The nozzle and injector body is manufactured as a matching pair and is accurately ground to give a good oil seal. The two are joined by nozzle nut.
The needle valve will open when the fuel pressure acting on the needle valve tapered face exerts a sufficient force to overcome spring compression.
The fuel then flows into the lower chamber and forces out through a series of tiny holes.
The number, diameter and angular position of the nozzle orifices are determined by the output of the engine and vary with different types of engines.
The fuel is atomized and injected into the combustion chamber where it will readily burn.
Once the injector pump cuts off the high-pressure fuel supply the needle valve will shut quickly under the spring compression force.
The degree of atomization and penetration is dependent on the viscosity of the fuel. If the viscosity is too high then atomization reduces and penetration increases.
If the viscosity is too low atomization increases and penetration decreases.
All slow-speed two-stroke engines and many medium-speed four-stroke engines are now continuously operating on heavy fuel.
A fuel circulating system is therefore incorporated within the fuel injector. When the engine is stopped the fuel booster pump supplies fuel which circulates around the injector body.
Some injectors is having internal cooling passages in them extending into the nozzle through which cooling water is circulating.
This is to prevent overheating and burning of the nozzle tip.
Injectors on modern 2 stroke crosshead engines do not have internal water cooling passages.
They are cooled by a combination of the intensive bore cooling in the cylinder head being close to the valve pockets and by the fuel which is recirculated through the injector when the follower is on the base of the cam or when the engine is stopped.
What is Sac?
The “Sac” is a small volume within the fuel flow path of a fuel injector.
It is defined as the volume between the valve seat (fuel shut off point) and the entrance to the final metering orifice of the injector
3. Cyinder Cover/Cylinder Head
Cylinder heads are exposed to maximum gas pressures and temperatures.
They must, therefore, have adequate strength and cooling. The combustion chamber may be formed by either shaping the cylinder cover or the piston crown.
The cover lands on the top of the cylinder liner flange and is secured to cylinder block by a number of cover studs and nuts.
These are tightened hydraulically to maintain a gas-tight seal.
The gas loads acting on the head are thus transferred to the cylinder block from which the tie bolts transfer it to the bedplate and then to the hull of the ship.
Properties of Cylinder cover material :
1. Must be of sufficient strength to withstand the gas load at maximum pressure.
2. Resist bending and be symmetrical in shape.
3. Have a rate of thermal expansion compatible with adjacent parts and transfer heat readily.
Material: Pearlitic or Nodular Graphite Cast Iron / Cast Steel.
Fittings: The design of heads is further complicated by the need to house various valves; fuel valve, air starting valve, relief valve, indicator valve/cock and exhaust valve.
As the cylinder head is exposed to a fairly high temperature the cooling water must also be at a reasonably high temperature, to avoid thermal stressing.
It is therefore usual to have the cooling water for the head in series with the jacket.
4. Tie Bolts/Tie Rods
Tie Bolts are one of the most important parts of a Two-Stroke Marine Diesel Engine Construction.
To hold the bedplates, frames and entablature firmly together in compression, and to transmit the firing forces back to bedplate, long tie bolts are fitted through these three components and then tightened hydraulically.
The compressive force they exert on these parts ensures that the tensile stress occurring during the peak pressure period is kept well below that could cause fatigue cracking.
The tie rods are made of ordinary mild steel and screwed at each end to take the nuts. These are positioned at each transverse girder.
To prevent excessive bending moments in the transverse girders, they are positioned as close as possible to the centre of the crankshaft.
Because tie rods are so close to the crankshaft, some engines employ jack bolts to hold the crankshaft main bearing cap in position, instead of conventional studs and nuts.
5. Crosshead
Two Stroke Marine Diesel Engine Construction consists of crosshead in its assembly.
The purpose of the crosshead is to translate reciprocating motion of the piston into the semi-rotary motion of the connecting rod and so bearings are required. The crosshead pin connects the piston rod to the connecting rod.
The crosshead pin sits in the crosshead bearing, which is either forked type where bearing housing is mounted on either side of the piston rod or of the continuous type where bearing housing is formed by the top of the connecting rod.
In the fork type, the piston rod passes through a hole in the crosshead pin and secured by a nut.
On the continuous type, the piston rod has a foot which is bolted onto the top of the crosshead pin. Modern diesel engines are fitted with a continuous type of bearings.
The bottom halves of the bearing shells have oil gutters cut in them to assist the distribution of oil.
Oil is supplied to the crosshead using a swinging arm or a telescopic pipe and is sometimes boosted in pressure to aid efficient lubrication.
The crosshead slippers are mounted on stepped journals machined either end of crosshead pins, secured in place by end plates.
The rubbing surfaces of the slippers are white metal lined. Oil is supplied to the slipper rubbing faces from the crosshead oil supply.
The slippers have gutters machined in them to assist the spread of lube oil.
The slippers run up and down in the crosshead guides as the piston and rod are reciprocating and prevent the top of the connecting rod from moving sideways.
This also ensures the piston remains central in the cylinder thus limiting wear in the liner.
why do Sulzer need to boost their crosshead oil supply pressure to 12 bar whilst MAN B&W supply oil to their crosshead at system pressure?
The answer lies in the design of the bearing.
More than 90% of the circulated oil has the sole purpose of cooling the bearings. for oil cooling.
In the main bearing, the oil is pumped into the upper shell and it will cool the upper part of the journal.
Since the shaft is rotating, it is cooled on all sides and because the oil film thickness is very small in the loaded part, the shaft will cool the loaded bearing half as well.
A crosshead bearing is only oscillating and the lower shell is always loaded. The cooling oil must be injected between the shaft (crosshead pin) and lower bearing.
In MAN B&W engines, a set of channels have been machined in the lower crosshead bearing, in which the cooling oil can pass.
The geometry is designed in such a way that all the loaded square centimetres of the pin are flushed with cooling oil twice every engine cycle. In contrast, the Sulzer crosshead has a plain lower bearing without channels.
In order to inject oil between pin and bearing, they have to supply oil at a much higher pressure. The injection will take place at around 20 degrees crank angle before TDC, where the cylinder pressure is still low and upward inertia forces on the piston are still high.
There is a short interval, in which the bearing pressure is lower than the oil pressure.
6. Connecting Rod
The connecting rod is fitted between crosshead and crankshaft and it connects the top and bottom end bearings. It transmits the firing force and together with crankshaft converts the reciprocating motion to rotary motion.
They are made from forged steel and shaped at each end to accommodate the appropriate bearings. On older engines, bearings were white metal thick wall bearings.
Clearances were adjusted by inserting or removing shims between the bearing halves.
Modern engines are of “thin-walled” type where
The clearance on this bearing is not adjustable when clearance reaches the maximum, bearings are changed.
An oil hole is bored through the Centre of the rod to allow passage of lubricating oil between the bearings – downward in crosshead engines but upward in trunk piston engines.
The length of the connecting rod is as short as the design allows, to limit the overall height of the engine.
Shorter the connecting rod, greater the angularity and larger the side thrust on the guides.
7. Liner
The lip of the upper part of the cylinder liner sits on a machined face at the top of the cylinder block and liner is held in place by cylinder cover.
This arrangement allows the liner to expand freely downwards when it is heated during the running of the engine.
Properties of Cylinder Liner Material:
1.Material for liners must provide adequate strength and fatigue life.
2.Resist abrasion and corrosion and must readily transfer heat.
3.Be able to retain a film of lubricating oil on working surfaces.
4.Have a rate of thermal expansion compatible with adjacent parts.
To meet these requirements, liners are cast in pearlite grey cast irons (contains graphite) to which alloying elements such as vanadium and titanium are added to enhance strength, wear, and corrosion resistance. Chrome-plated liners have an extended life, but the initial cost is higher.
The liner must satisfy the contradictory requirements of being thick and strong enough to withstand high temperature and pressures that occur during combustion and thin at the same time to allow heat transfer.
This is achieved by bore cooling. Boring is carried out in the upper part of the liner at an angle to the longitudinal axis by which the cooling water is led close to the combustion space area.
By using this technique of bore cooling good heat transfer and high overall strength is achieved.
A cooling water space is provided between the cylinder block and liner and this space is sealed at its lowest part by means of silicon rubber ‘O’ rings.
Sealing is provided by two rings, the upper one for sealing cooling water space and the lower one to seal scavenge air.
A telltale hole is provided between two rings to indicate leakage of cooling water or air.
Scavenge airports are cut in the lower section of the liner and these ports are machined at an oblique angle to the axis of the cylinder in order to impart a rotary motion to scavenge air.
Oil is injected through a number of holes drilled in the liner, usually, 6 or 8, located circumferentially around the liner.
Lubricator quills are connected to the oil holes and each contains a non-return
valve to prevent the blowback of gases.
8. Piston
The Construction of Two-Stroke Marine Diesel Engine consists of a piston which converts the force produced by the combustion gases to mechanical power through its reciprocating motion.
The Piston is usually of composite construction consisting of Piston crown and skirt.
Crown: The shape of the crown is generally concave to give an efficient combustion space.
Properties of Piston Crown material:
1. High mechanical strength to withstand the high gas load.
2. Long fatigue life to survive the fluctuating mechanical and thermal stress.
3. High thermal conductivity and low coefficient of expansion.
4. High surface property i.e. hardness, anti-corrosive.
5.The metal must resist high-temperature corrosion and erosion.
The piston crown is cast in chromium – molybdenum alloy steel. Chromium, molybdenum and nickel are added for strength, heat resistance and higher thermal conductivity.
In some MAN B&W Engines, Piston has 8 mm thick heat-resisting a layer of a hard nickel-chrome alloy called Inconel, welded to the hottest part of the crown to resist the “burning” of a crown.
The crown has 4 or 5 piston ring grooves which are chromium plated to resist the wear. The layer thickness is increased suitably to give higher corrosion resistance.
Skirt:
The skirt acts as a guide within the cylinder liner. It is usually made of cast iron as the mechanical and thermal load acting on the skirt is much less as compared to a crown.
The skirt is much smaller in modern engines, as the side thrust due to the connecting rod angularity is taken up by the crosshead guide and guide shoes.
Soft bronze rings are also fitted in the piston skirts.
These bronze rings help during the running-in of the engine when the engine is new and can be replaced if necessary.
Piston Rod
Piston rods help in transmitting the power produced in the combustion space to the crosshead and the running gear of the engine.
The lengths of these rods depend on the length of the engine stroke and the manufacturer’s design.
The top-end of the rod is flanged or attached to the underside of the piston and the bottom end is connected to the crosshead.
Material: forged steel / cast steel
Piston Cooling
Cooling of the piston is necessary to remove excess heat from combustion and to limit thermal stress. Modern engines have oil-cooled pistons.
The piston rod is utilized to carry the oil to and from the piston. The rod is hollow and has a tube running up its centre.
Oil is forced through the telescopic pipe via crosshead and piston rod to an annular space around the groove.
It returns via the crosshead to a collector where its flow and temperature are monitored.
An alternative method of cooling uses a nozzle plate and nozzles.
The oil goes up the annular space formed between the oil tube and bore in the piston rod, and returns down the centre.
The oil is sprayed up onto the underside of the crown.
This allows the crown to be made as thin as possible, to allow for maximum heat transfer while maintaining strength, and combined with cocktail shaker caused by the reciprocating motion, giving efficient cooling.
9. Piston Rings
The function of a piston rings is to:-
1) Provide a seal to the combustion chamber, by expanding outwards due to gas pressure acting behind them. They prevent the gases and combustion products passing the piston.
2)Conduct heat away from the piston to the liner.
3)Control the lubricating oil.
Properties of Piston Ring material:
1.Highly mechanical strength and good tension properties.
2.Elasticity and wear resistance with low-friction.
3.Must be corrosion resistance.
4.Must be resistance against high temperature.
5.Self-lubricating properties.
6.Must readily transfer heat and compatible with cylinder material.
7.Compatible with piston for thermal expansion to maintain ring groove clearances.
Piston rings are made of cast iron alloy with chromium, molybdenum, vanadium, titanium, nickel, copper.
The top ring which is subjected to the greatest load and temperature, maybe chrome or plasma plated. Ring clearances are necessary to allow movement and thermal expansion.
Reasons for failure of Piston rings:
1. Insufficient piston ring groove clearances causing the ring to jam in the groove.
2. Insufficient lubrication causing abrasive wear.
3. Excessive wear/ovality of liner
4. Ring gap inadequate leading to breakage.
10. Crankshaft
The crankshaft is the backbone of diesel engines and transmits power from the cylinders to the propeller shaft. Strength and rigidity are essential features of any crankshaft design.
The crankshaft is subjected to fluctuating bending, torsion and shear stresses.
The material used must have:-
The material used for manufacture of the crankshaft is-
Types of crankshafts :
There are various types of crankshaft available, each having their own advantages and dis-advantages.
Let’s learn about all types of crankshaft.
1.One piece construction:
Either cast or forged is usually restricted to smaller medium and high-speed engines.
After casting or forging operation, the crankshaft is machined and oil passages are drilled.
Advantages:
2.Fully Built-Up:
Webs are shrunk onto journals and crankpins.
These types of crankshafts were mainly used on older engines. They consist of forging separate webs, crankpins and journals.
The crankpins and journals are machined and matching holes bored in webs of slightly smaller diameters.
The webs are heated up and cooled slowly to shrunk fit on crankpin and journals.
3. Semi Built-Up:
Webs and crankpins as one unit shrunk onto journals.
In this method of construction, the crankshaft throws consisting of two webs and crankpin are made from a single forging of 0.4% Carbon steel.
The webs are bored to take separately forged and machined journals which are shrunk fit. The shrunk fit allowance is between 1/570 and 1/660 of the diameter.
The advantage of this method is that the grain flow in the steel follows the web round into the crankpin and back down the other web.
4. Welded construction:
Has cast steel units comprising web, half crankpin and half journal pin or it can be a series of forgings each comprising of half journal, web, crankpin, second web and half journal.
These are welded together at journals and crankpins to form one complete crankshaft. After welding the journals are stress relieved and machined.
The advantage of the welded crankshaft–
11. Camshaft
In a Two-Stroke Marine Diesel Engine Construction, a camshaft is necessary to operate the exhaust valves and fuel pumps which control the engine cycle.
Each valve or the pump is operated by a cam follower which rises or falls as the cam rotates beneath it.
The profile or shape of each cam is designed to give the correct timing, speed and height of lift to its corresponding follower.
Camshaft may consist of a number of part lengths joined at flanges with fitted bolts.
Each part length will have a set of cams for one unit. Each part length may be dismantled separately to simplify overhaul, repair or adjustment.
The individual cams are manufactured from steel which are heat-treated to give them a very hard surface. The cams are expanded onto the camshaft using either heat or hydraulically.
The whole shaft must be rigidly supported with white metal lined bearings, lubricated in most cases by main engine LO system.
Some engines have a separate camshaft lubrication system to prevent any possibility of fuel leakage from pumps passing into the crankcase oil.
In a two-stroke engine as exhaust valve and fuel pumps are operated once every cycle, the camshaft rotates at the same speed of the crankshaft.
They have fewer cams since they do not require air inlet valves and loop and cross scavenging do not need exhaust cams.
It is very important that the fuel pump and exhaust valve operate at exactly the right time, so the camshaft is driven by the crankshaft.
Two methods are used, a gear drives in case of Sulzer engines and chain drive, in case of B&W engines.
Chain drives are relatively light, narrow in width and flexible. However, they elongate in service due to wear which will affect the camshaft timing and they have a limited life of about 15 years.
Gear drives should last the life of the engine, however, gear train is heavier and more expensive.
12. Frame Box/A-Frame
In crosshead type engines frames or columns are used to support the cylinder block from the bedplate.
They are termed ‘A” frame because of their shape and are fitted at each transverse girder.
The frame box is a single welded unit for large bore models and a cast-iron unit for smaller types, the design contributing to a very rigid engine structure.
These carry the crosshead guides and support the engine entablature (cylinder block). The guide surfaces are either machined into the A-frames or are separately cast and machined, then bolted to the A-frames.
In modern engines, the frame box is built as a separate fabricated construction and then, after stress relieving and machining the mating surfaces are mounted on the bedplate.
This has the advantage of saving weight. When the frames are aligned on the bedplates they are secured together by drilling and using fitted bolts.
The frame box is equipped on the exhaust side with a relief valve and on the camshaft side with a large door for each cylinder providing access to crankcase components.
In medium-speed engines, the main strength member may consist of a single frame or block which incorporates the crankcase, bedplate, frames and cylinder block.
These may be formed as a single casting of nodular cast iron (ductile cast iron which is more flexible and elastic) or fabricated from steel plates and castings.
13. Entablature/Cylinder Block
The entablature is the name given to the cylinder block which incorporates the scavenge air space and the cooling water spaces.
It forms the housing to take the cylinder liner and is made of cast iron.
The castings are either for individual cylinders which after machining on the mating surfaces are bolted together to form the cylinder beam, or they may be cast in multi-cylinder units, which are then bolted together.
The underside of the cylinder beam is machined and then it is aligned on the A-frames and fastened in position using fitted bolts.
14. Bedplate
Construction of Two-Stroke Marine Diesel Engine consists of Bed-Plate at the bottom.
The bedplate is the foundation on which 2 stroke engine is built. It must be rigid enough to support the weight of the engine components and maintain the alignment of the crankshaft.
At the same time, it must be flexible enough to be capable of withstanding the fluctuating forces created during operation and transmit them to the ship’s structure.
The bedplate consists of two longitudinal girders which run the length of the engine.
Connecting these longitudinal girders are transverse girders which are positioned between each crank throw, and either side of thrust collar.
Built onto these transverse girders are cast steel bearing supports. The crankshaft sits in the bearing housing in the transverse girders.
The aftmost transverse girder is designed with ample stiffness to transmit the variable thrust from the thrust collar to the engine seating.
On smaller bore engines, bedplate can be made from cast iron as a simple casting.
Cast iron has internal resilience allowing it to dampen down vibrations, this has led to its usage on some medium speed installations.
The bedplate of the modern engines is constructed from fabricated longitudinal girders with cast steel transverse sections welded into place, containing the bearing pocket and holes for tie bolts.
The bedplate should be inspected regularly for evidence of cracking.
This can occur in the welds joining the transverse girders to the longitudinal and under the bearing pockets.
Inspection should be carried out especially after heavy weather or damage has occurred.
Causes for cracks can be
1. ENGINE STRUCTURE – INTRODUCTION
1. REQUIREMENTS OF THE ENGINE STRUCTURE
2. ENGINE STRUCTURE’S TRANSVERSE STRENGTH
3. ENGINE STRUCTURE’S LONGITUDINAL STRENGTH
2. ENGINE STRUCTURE FRAME
1. TOP BRACING
This is usually of mechanical or hydraulic type, fitted to the top part of the engine to provide stiffening and support against twisting forces from the crosshead guide. Normally, these braces are fitted to only one side of the engine e.g. the exhaust side.
2. ENTABLATURE