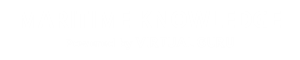
Design of Marine Machinery
In the basic design of Marine Machinery for main propulsion, the following points to be considered.
What type of Main propulsion Engine do we need? That depends on a number of factors, Cost of the engine and its delivery schedule; to be able to match the ship construction work in progress; designed machinery space available on the ship; the overall plant efficiency; specific fuel oil consumption; compliance to current and near future environmental restrictions for emissions; operating costs including spares and their ready availability; and issues involving important components like Turbocharger, Governor, the auxiliary engines and so on.
In many cases, the shipowners experience with a type of engine also makes a big difference; if a shipowner has deep experience with a particular slow-speed engine, it is unlikely that he will go for another. The company tends to build upon the skills of its workers and would feel uncomfortable introducing a different engine, e.g., just to save 0.5% of fuel economy. That is the reason the engine makers always try to introduce a new version of an engine at a discounted pricing until, the engine type has proven its worth on board. It took no less than 5 years for the super-long-stroke engines to gain its acceptance.
So, if new Technology is to be used, question will be, are they proven? And, are the current Maine Engineers capable of managing these engines or, would they require extensive additional training? These are the dilemmas of a shipowner.
Based on these points and mainly on the propulsion characteristics, either a diesel engine, with the latest available proven technological improvements or a COGES system (as the one seem to be a current preference) -- Again, initial cost plays a major role, One needs to pay more for the latest technologies. An alternator coupled with a Turbocharger which uses exhaust gas as a normal turbocharger, but also takes care of the complete electrical load, when the main engine is running; this combination was costing less, when it was introduced in the market; for the same engine system: the cost is more than doubled after it has been a success in the first few ships.
Since it is very important that the Engine and the propeller are correctly matched, their selection often goes in tandem. We can decide on the diesel engine and the propeller type- fixed pitch or variable pitch based on the availability of space where the machinery layout plays an important part. But the more popular choice today, for the larger ships demanding higher power , is to go for long stroke slow speed engine. Even if the vessel is not placed on a liner run and must tramp as demanded by the market. The winner here is the lower fuel consumption and ability to manipulate speed within a reasonable range with optimum efficiency. Whereas, if a LNG carrier is built, on a contract covering the life cycle period of the engine; and, with assured loading and discharge ports on fixed voyages; that commercial assurance, will certainly play a major role in selection of the main propulsion machinery, where new innovation can be supported with lesser commercial risks.
Improvement in Design
Engine manufacturers have been busy with a number of design improvements over the last decade; some of those are contribution from,
Ships Engines and propulsions: 2 and 4 stroke
High bmep increases the stresses on nearly all the engine components, with a consequently greater rate of cylinder wear, whilst the alternative of higher speed, valve flutter may become a serious problem.
But the 2 stroke engines have many more advantages,
The 4-stroke engine have good volumetric efficiency, Good combustion characteristics, Positive exhaust scavenging and a less arduous lubrication requirements due to the presence of an idle stroke which allows spread of lubricating oil through bearings and around the liner. The thermal and mechanical efficiency are slightly better than those of two-stroke engine. In this type of engines only half the quantity of the heat generated in the cylinders has to be dealt with a given time, so that efficient lubrication of the piston and cooling of the cylinder is more easily accomplished.
The followings are also advantages of using four stroke engines:
In conclusion it can be summarized, that from a purely efficiency and usefulness point, both 2 stroke and 4 stroke engines have made their presence felt within the maritime sector. In that larger vessels have been using slow speed 2 stroke, whereas the smaller vessels made use of the 4-stroke engines, which due to their higher speed could generate higher power and did not need a lot of space. Thus, the choice has been largely driven by commercial suitability.
The current trend toward newer plant designs with combined cycles and better Waste Heat Recovery and also with electric propulsion initiatives, the medium speed engines could become a strong contender. The push for burning better fuel and gas could also tip the balance toward more application of the 4-cycle and even higher theoretical efficiency in gas burning via Otto cycle is on vogue.
Wärtsilä and MAN- B&W are the foremost license providers across the globe; in 2015, they accounted for more than 95% of the global low speed engine market share and over 75% of medium speed engine market share. At present, Japan, China, and South Korea collectively account for over 80% of the regional marine diesel engine market size..Global marine diesel engine market size was valued at around USD 6 billion in 2015 and is anticipated to exceed USD 8 billion by 2023, with growth rate at over 4% from 2016 to 2023.
Industry Analysis
Marine Propulsion Engine Market size was over USD 9 billion in 2015, and is anticipated to grow at 4.3% CAGR from 2016 to 2024.
Copyright VIRTUAL GURU © 2025. All Rights Reserved.