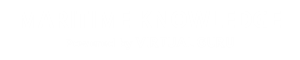
Theory of Maintenance
Introduction
We are all aware that the two fundamental areas governing a sailing marine engineer’s domain of activity, are
In this topic we will discuss various basic philosophies concerning the theory of maintenance and while the marine engineer is seldom made to think of the philosophies, rather than follow strictly as per the company directives and the Class rules, new technology has brought forward new hopes for monitoring of machinery and its needed maintenance, just-in-time, based upon perhaps a trend analysis technique etc. So, it makes sense to have a deeper thought in terms of what we do, and why we do that? That is truly the essence of Theory of Maintenance.
The shipboard maintenance regime has developed historically, as guided by the Classification Societies and shipping companies experiences in operating their individual fleets. The Class societies, imposed an inspection and certification process on equipment and machinery which they insisted upon and the responsible shipowners also introduced company specific maintenance plans that went beyond the requirement of the Class. In recent times, more regulatory and professional bodies have further imposed their influence in number of shipboard operating areas. But the underlying philosophy must be based on uninterrupted operation of the ship without any unplanned "downtime" that affects commercial interest. This is done in majority of shipping, as a time-based maintenance plan, supported by the Class requirements. The maintenance is divided for annual, intermediate and certification survey, extending over 5 year period. There is a move to extend the timeframe, using a more elaborate risk based assessment using higher technologies.
Copyright VIRTUAL GURU © 2025. All Rights Reserved.